Fiddleback
Well-Known Member
On another forum I was asked me to run down how I make my handles. So here it is. First I choose two woods that I think would contrast nicely together. Then I go to my tablesaw.
I rip the liner wood ~1/8" thick, and the outter wood 1/4" thick for a 3/8" thick scale. Usually my tablesaw does a fine job, and I can go right to glueup, but if there is doubt I go to plate glass and sandpaper.
I use spray adhesive to glue 60 grit paper to the glass, and a no skid cabinet liner thingie to make sure it doesn't slide around on me. Make sure you sand as little as possible here. You want to avoid making the faces un-paralell. Use a circular or figure 8 motion, so that your sanding pattern is swirley. Once the surfaces are lapped, check for fit by holding the two pieces of wood together and trying to see light between them.
1/4" thick Cocobolo, and 1/8" thick Osage.
Don't try to glue it up all at once. I use epoxy between the wood layers, and superglue for the wood to vulcanized fibre liner. The superglue soaks into the fiber liner better, and gives a much better bond. This pic is of a stackup.
Rosewood over Maple with brick red fibre liner.
Thats as far as I got today. I burned myself with a red hot blade yesterday, and couldn't do any real work today. More tomorrow, but from here you pretty much treat the block as normal scale material.
Questions and comments welcome.
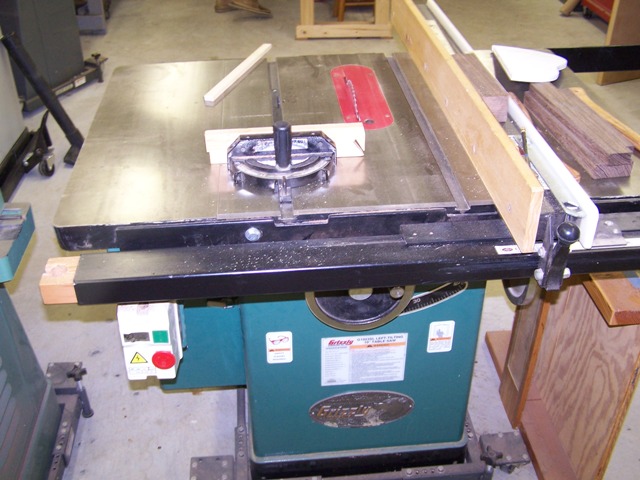
I rip the liner wood ~1/8" thick, and the outter wood 1/4" thick for a 3/8" thick scale. Usually my tablesaw does a fine job, and I can go right to glueup, but if there is doubt I go to plate glass and sandpaper.
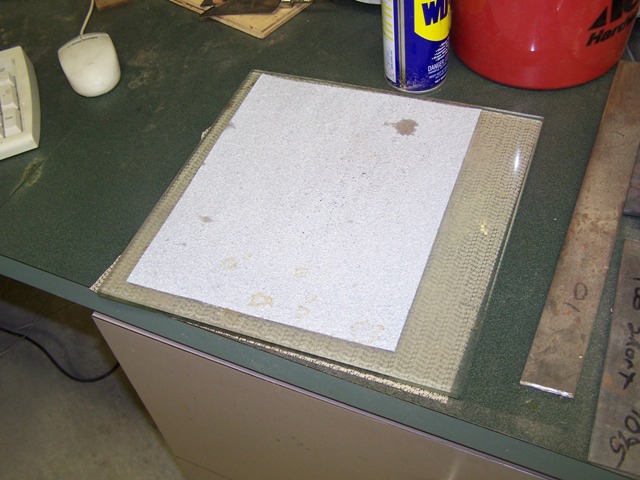
I use spray adhesive to glue 60 grit paper to the glass, and a no skid cabinet liner thingie to make sure it doesn't slide around on me. Make sure you sand as little as possible here. You want to avoid making the faces un-paralell. Use a circular or figure 8 motion, so that your sanding pattern is swirley. Once the surfaces are lapped, check for fit by holding the two pieces of wood together and trying to see light between them.
1/4" thick Cocobolo, and 1/8" thick Osage.
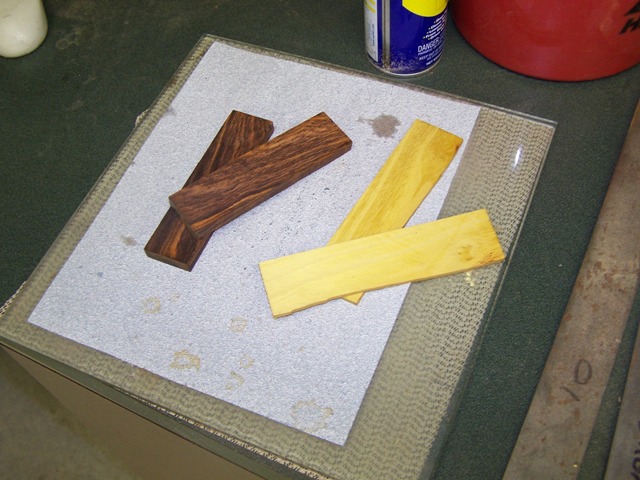
Don't try to glue it up all at once. I use epoxy between the wood layers, and superglue for the wood to vulcanized fibre liner. The superglue soaks into the fiber liner better, and gives a much better bond. This pic is of a stackup.
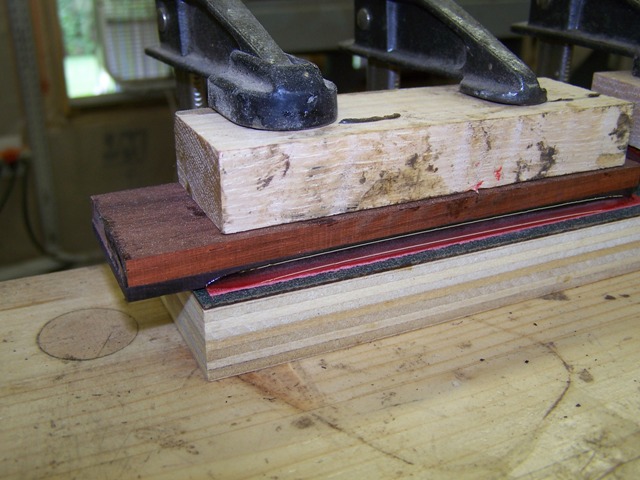
Rosewood over Maple with brick red fibre liner.
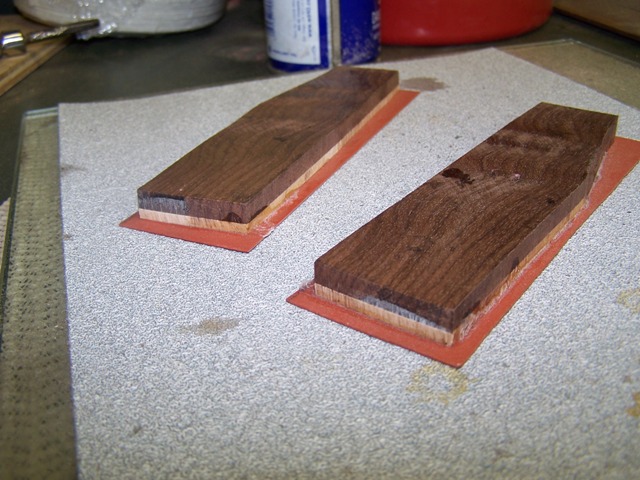
Thats as far as I got today. I burned myself with a red hot blade yesterday, and couldn't do any real work today. More tomorrow, but from here you pretty much treat the block as normal scale material.
Questions and comments welcome.