kevin - the professor
Well-Known Member
Greetings Everyone,
this is truly a work-in-progress. However, it has made it through heat treatment, so I think it is safe to show the progress thus far. I am really enjoying these steels. They weld together well, have good contrast, and have similar heat treating characteristics.
Plus, they are quite tough and hold a good edge. I don't have metallographic capacity, or even a Rockwell tester, so I admit my testing is limited. Still, they seem to work well together, though they require some special treatment due to a tendency to air harden a bit coming out of the forge. There are some additional heating and cycling requirements when forging compared to the simpler steels. But, I think they are worth it.
Here goes:
these are the bars stacked and ready to be forge welded. No flux was used to weld these. There are two that are thicker stacks than the other two. These will be longer, and be the spine of the blade, and have more 15n20. The two bars nearer the edge are shorter and have less 15n20. The overall blade is mostly 80crv2, then o1, then 15n20 (about 3.5:2:1)
Welded and drawn, shaped into octagons for twisting. They are about .75" diameter.
New anvil stand needed a pic. Compare to the plastic bin full of dirt that the anvil was in. This can be seen in the first photo. I took time out to get my anvil the right height and well-supported before continuing the project. Cool, huh?
Gettin' down to business with the twist-o-matic 3000! This is something I made (and you should make one, too!). The little forge will reach a serious welding heat for about 1.5" or so. It just sips propane, too. I have it mounted on a post-and-rail assembly (parts = two nearly identical square tubes, one fits just over the other, box of nuts, box of bolts, forge, mild steel plate for mounting forge to post, and one firebrick forge).
Bring the bar up to welding heat, twist, slide the forge down the rail 1" (that is what the chalk marks are for, to get even twists). Repeat. It is dead simple, and you can get tight twists that are structurally sound. I think that I am really welding while twisting. You really should make one of these!
These are actually bars from a bowie knife project, but they look almost the same as the bars from the current project. Only difference is that I cut the end off of one of the bars in the bowie set, and the ones for the messer are a little thicker. But, I didn't get pics of them at this point, so the bowie set will have to do.
thanks for looking. I hope you enjoy the ride. Wish me luck.
this is truly a work-in-progress. However, it has made it through heat treatment, so I think it is safe to show the progress thus far. I am really enjoying these steels. They weld together well, have good contrast, and have similar heat treating characteristics.
Plus, they are quite tough and hold a good edge. I don't have metallographic capacity, or even a Rockwell tester, so I admit my testing is limited. Still, they seem to work well together, though they require some special treatment due to a tendency to air harden a bit coming out of the forge. There are some additional heating and cycling requirements when forging compared to the simpler steels. But, I think they are worth it.
Here goes:
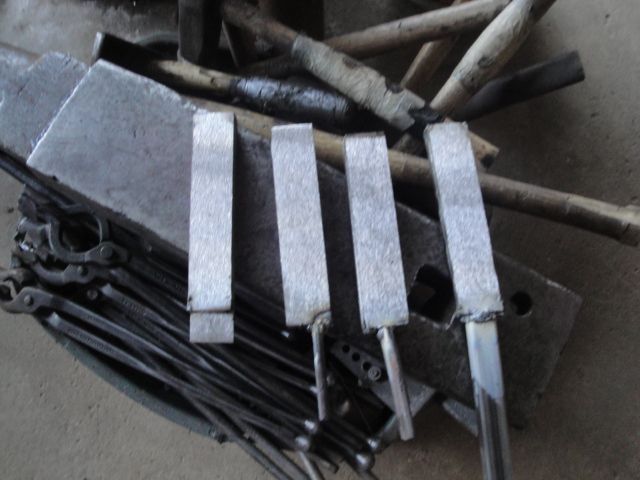
these are the bars stacked and ready to be forge welded. No flux was used to weld these. There are two that are thicker stacks than the other two. These will be longer, and be the spine of the blade, and have more 15n20. The two bars nearer the edge are shorter and have less 15n20. The overall blade is mostly 80crv2, then o1, then 15n20 (about 3.5:2:1)
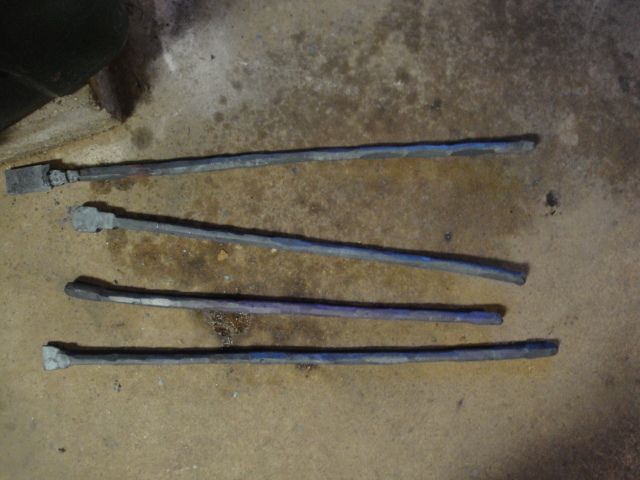
Welded and drawn, shaped into octagons for twisting. They are about .75" diameter.
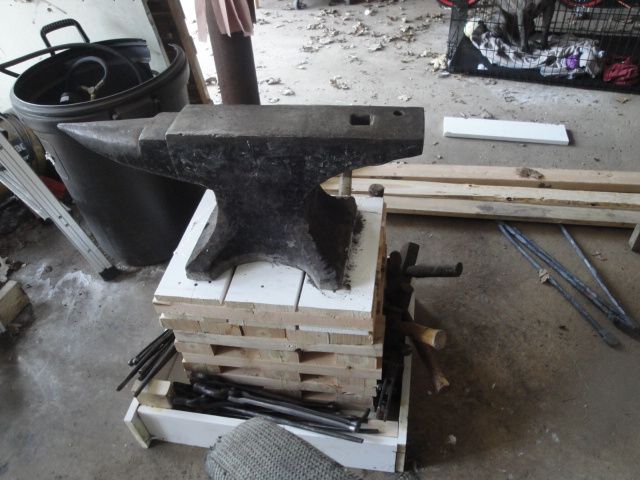
New anvil stand needed a pic. Compare to the plastic bin full of dirt that the anvil was in. This can be seen in the first photo. I took time out to get my anvil the right height and well-supported before continuing the project. Cool, huh?
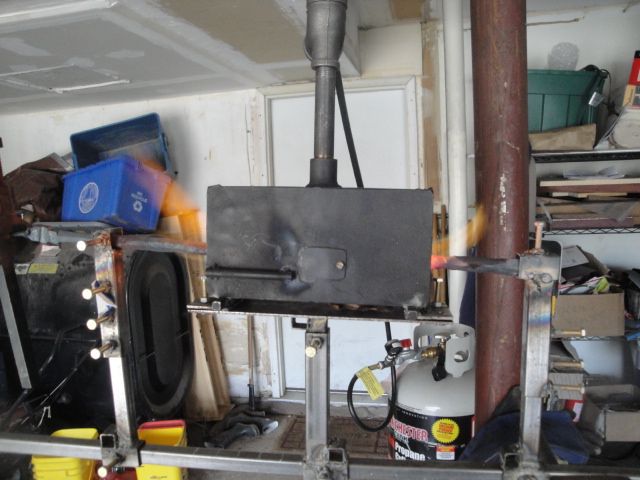
Gettin' down to business with the twist-o-matic 3000! This is something I made (and you should make one, too!). The little forge will reach a serious welding heat for about 1.5" or so. It just sips propane, too. I have it mounted on a post-and-rail assembly (parts = two nearly identical square tubes, one fits just over the other, box of nuts, box of bolts, forge, mild steel plate for mounting forge to post, and one firebrick forge).
Bring the bar up to welding heat, twist, slide the forge down the rail 1" (that is what the chalk marks are for, to get even twists). Repeat. It is dead simple, and you can get tight twists that are structurally sound. I think that I am really welding while twisting. You really should make one of these!
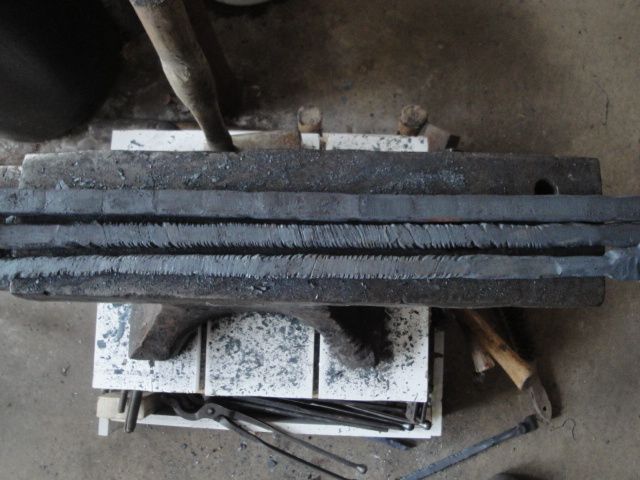
These are actually bars from a bowie knife project, but they look almost the same as the bars from the current project. Only difference is that I cut the end off of one of the bars in the bowie set, and the ones for the messer are a little thicker. But, I didn't get pics of them at this point, so the bowie set will have to do.
thanks for looking. I hope you enjoy the ride. Wish me luck.