J S Machine
Well-Known Member
Hey folks. It's been a while since I have been a regular around here. My work schedule keeps me just far enough away from my knives to be able to do them as much as I'd like, so not much comes out of my shop. I do, however, try to reserve time for at least one a year. That knife is donated through another forum I'm a part of to benefit St. Jude Children's hospital. This is a cause that is very important to me, because these sick children need as much help as they can get.
This WIP will be for a Sub hilt style fighter. I did a WIP for last year's knife on the forum that this knife will be auctioned on, and it was a big hit. I already started a WIP thread there, and I figured here could possibly benefit anybody who might wonder about this style.
Randy Haas (HHH Knives) was the source for two of the materials for this knife. He provided to Tsunami pattern damascus bade blank, and also the fossil mammoth Ivory for the scales. I can do many things, but I don't forge my own steel or damascus. The reason is because I don't have the time or space to put in a power hammer or anvil and the neighbors would never put up with the noise...
Anyway, Randy's Tsunami pattern damascus is made from 1080 and 15N20 steels. You should be able to see a little of the pattern in this first picture.
Paul Long usually makes my sheaths, but he is swamped right now. Looking through the forum here I found the guys from Rowe's leather in Hope, AR. I gave them a call and asked if they would be interested in doing a sheath and they said they would be glad to.
I was having trouble trying to decide on a design and was talking with Rex about this. You may know Rex here on the forum as McClellan Made Blades. I was telling him how I really liked fighters. I have never done a knife with a guard. I don't have any particular reason for that, other than that I've just never tried it. Rex told me he thought I should do a fighter, so I think I will.
Now, what kind of fighter? I had an idea. I have been a big fan of everything Bruce Bump does since the day I started doing knives (can we get around of applause for Bruce!), so I went to his forum. After looking around there for a bit, I decided I really liked the Bob Loveless Sub Hilt design knife. He did a WIP for one there, and mine will closely follow his.
One of the things Bruce and I talked about was that if you do a knife like a Bob Loveless Sub hilt, it really needs to be an exact copy. I don't have that much steel. I think his was around 14" overall length, and my steel from Randy is only about 11" or so. Since this is the case, this knife will look somewhat like the Bob Loveless version, but with some of my own touches.
This style blade actually has a double grind on top and bottom, with the top being a false edge. I was talking with Bruce about all of this. Grinding blade profiles has never been one of my strong suits. I can do it, but it is extremely hard for me. I guess being good at it comes after a lot of experience and practice. At this point, Bruce offered to do the heat treating and blade grinds and jump in to a collaboration effort. I am honored that he would even offer to do this. After thinking about it, I decided to try that double grind. I'll never know if I can do it unless I try, right?
This WIP will be for a Sub hilt style fighter. I did a WIP for last year's knife on the forum that this knife will be auctioned on, and it was a big hit. I already started a WIP thread there, and I figured here could possibly benefit anybody who might wonder about this style.
Randy Haas (HHH Knives) was the source for two of the materials for this knife. He provided to Tsunami pattern damascus bade blank, and also the fossil mammoth Ivory for the scales. I can do many things, but I don't forge my own steel or damascus. The reason is because I don't have the time or space to put in a power hammer or anvil and the neighbors would never put up with the noise...
Anyway, Randy's Tsunami pattern damascus is made from 1080 and 15N20 steels. You should be able to see a little of the pattern in this first picture.
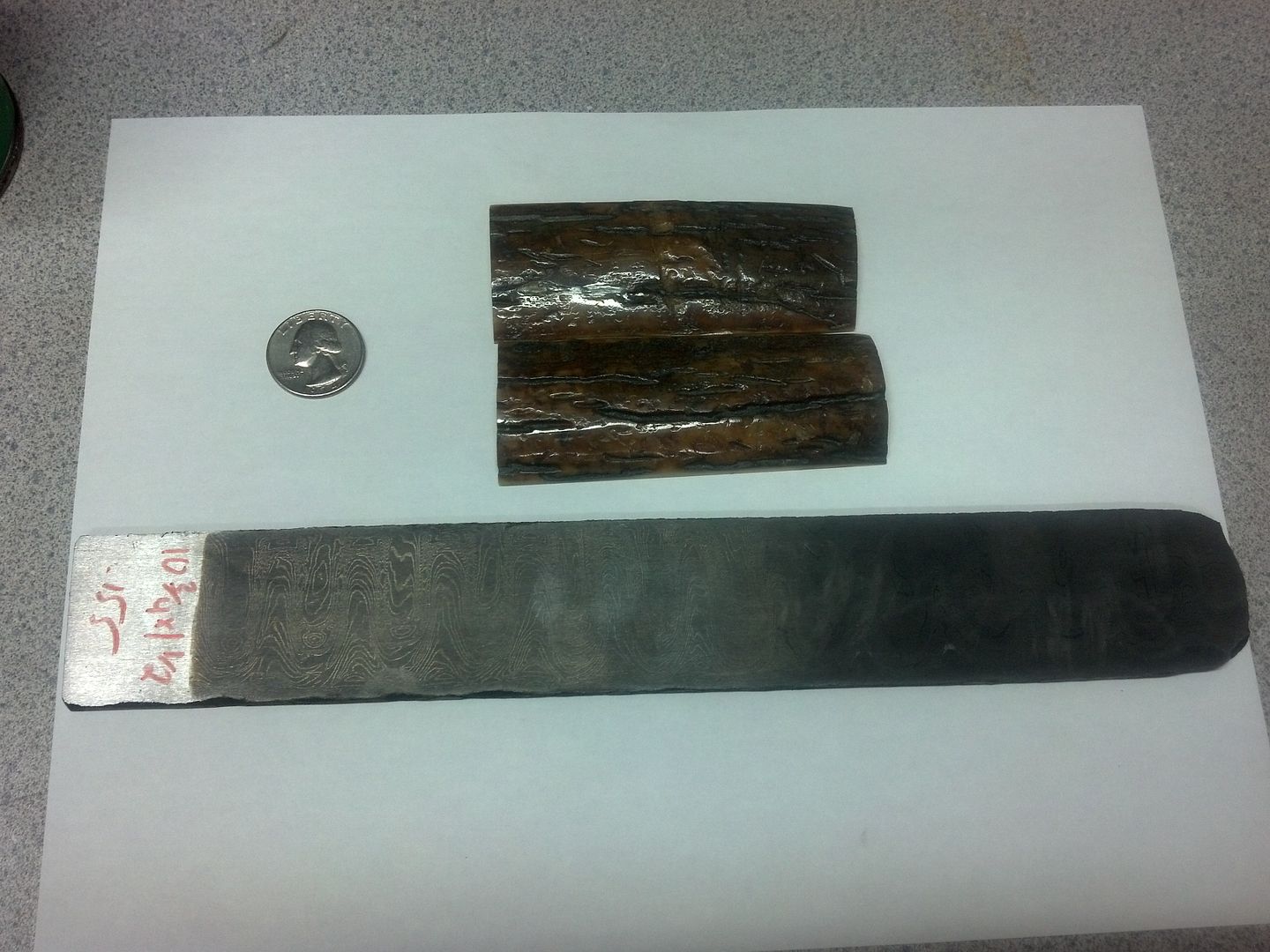
Paul Long usually makes my sheaths, but he is swamped right now. Looking through the forum here I found the guys from Rowe's leather in Hope, AR. I gave them a call and asked if they would be interested in doing a sheath and they said they would be glad to.
I was having trouble trying to decide on a design and was talking with Rex about this. You may know Rex here on the forum as McClellan Made Blades. I was telling him how I really liked fighters. I have never done a knife with a guard. I don't have any particular reason for that, other than that I've just never tried it. Rex told me he thought I should do a fighter, so I think I will.
Now, what kind of fighter? I had an idea. I have been a big fan of everything Bruce Bump does since the day I started doing knives (can we get around of applause for Bruce!), so I went to his forum. After looking around there for a bit, I decided I really liked the Bob Loveless Sub Hilt design knife. He did a WIP for one there, and mine will closely follow his.
One of the things Bruce and I talked about was that if you do a knife like a Bob Loveless Sub hilt, it really needs to be an exact copy. I don't have that much steel. I think his was around 14" overall length, and my steel from Randy is only about 11" or so. Since this is the case, this knife will look somewhat like the Bob Loveless version, but with some of my own touches.
This style blade actually has a double grind on top and bottom, with the top being a false edge. I was talking with Bruce about all of this. Grinding blade profiles has never been one of my strong suits. I can do it, but it is extremely hard for me. I guess being good at it comes after a lot of experience and practice. At this point, Bruce offered to do the heat treating and blade grinds and jump in to a collaboration effort. I am honored that he would even offer to do this. After thinking about it, I decided to try that double grind. I'll never know if I can do it unless I try, right?
Last edited: