Mike Martinez
Well-Known Member
Where to start, this one. About a month ago I grew tired of my sears grinder and decided to get one of the Bader Clones in the way of the EERF grinder. I sourced it out to a local company that couldn't meet a deadline and depleted me of all patience and confidence in their ability. They made multiple attempts at cutting it and failed miserably each and every time. Thankfully, my wife caught me looking at Jamie's site and "suggested," that I call the local guys and "fire them." Advice taken.
I emailed Jamie on a Friday and placed my order, lo and behold, it was at my door today at the same time that my Leeson 2hp 3ph Motor arrived. Happy me! I've been playing with it for the past hour or so before this post, and took some pictures of the mock-up aimed to see if a 145TC motor would be interchangeable with the 56C. Well, all but my decision to go with a 7/8 shaft was identical.
After coming down from the initial high that accompanies a new toy, the camera came out and some shots were taken. Bellow is my slow progress in a 115 degree Texas garage.
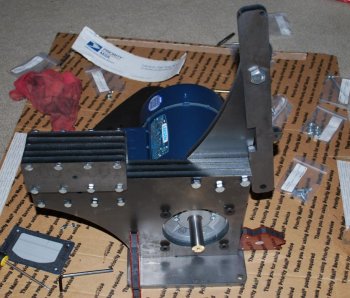
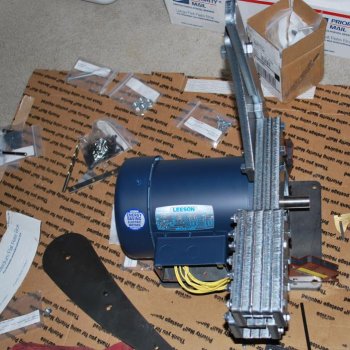
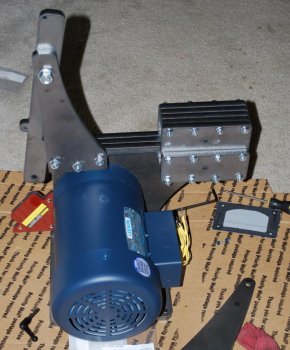
I emailed Jamie on a Friday and placed my order, lo and behold, it was at my door today at the same time that my Leeson 2hp 3ph Motor arrived. Happy me! I've been playing with it for the past hour or so before this post, and took some pictures of the mock-up aimed to see if a 145TC motor would be interchangeable with the 56C. Well, all but my decision to go with a 7/8 shaft was identical.
After coming down from the initial high that accompanies a new toy, the camera came out and some shots were taken. Bellow is my slow progress in a 115 degree Texas garage.
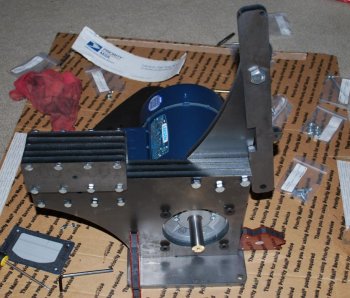
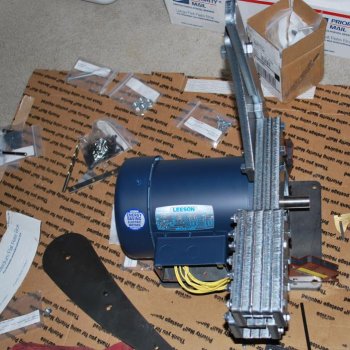
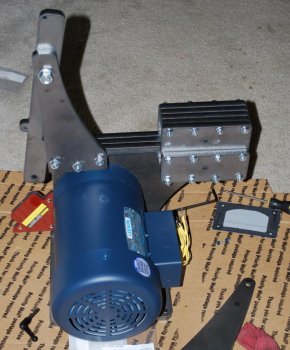