SHOKR
Well-Known Member
I dont know exactly whats its called
But it happens when any part or the profile is ground parallel to a wheel (i am guessing this happens due to the welded part)
Any idea how prevent or deal with that? Aside from the obvious hand sanding of course
If it just hand sanding, at which grit do you start?
Thanks
update:
adding example of one the areas i am talking about
i tried taking several photos, non show them so well, but i meant parts like the belly of tang, its top and the spine of the blade
the part of the reflection at the top is actually due to a 'dent', the ones i am asking about
But it happens when any part or the profile is ground parallel to a wheel (i am guessing this happens due to the welded part)
Any idea how prevent or deal with that? Aside from the obvious hand sanding of course
If it just hand sanding, at which grit do you start?
Thanks
update:
adding example of one the areas i am talking about
i tried taking several photos, non show them so well, but i meant parts like the belly of tang, its top and the spine of the blade
the part of the reflection at the top is actually due to a 'dent', the ones i am asking about
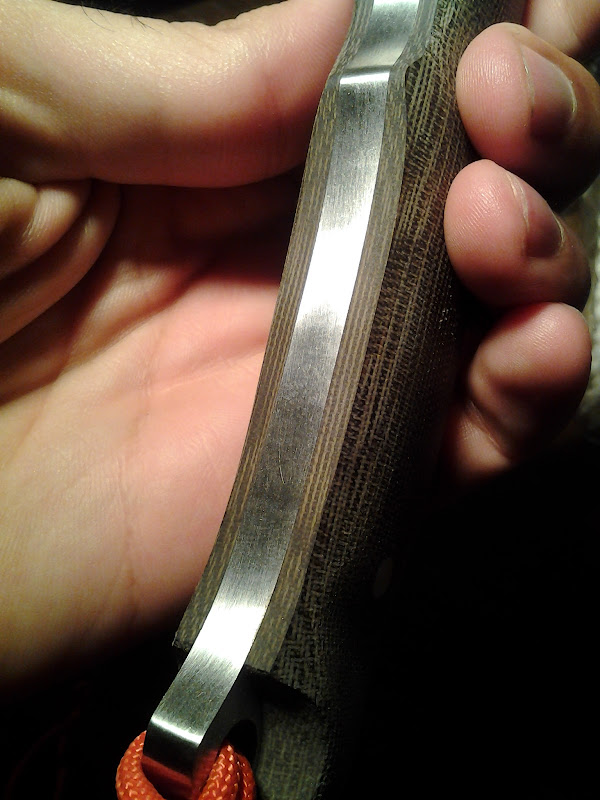
Last edited: